The global shift towards clean energy has led to an increasing demand for electric vehicles (EVs) and renewable energy storage solutions. As a result, the production of lithium-ion batteries has skyrocketed in recent years, with Tesla’s Gigafactory leading the charge. However, experts are now warning of a potential supply cliff for battery raw materials as Gigafactory demand continues to build.
The Gigafactory, located in Nevada, is Tesla’s massive factory dedicated to the production of batteries for EVs and energy storage. With an annual production capacity of 35 gigawatt-hours, it is currently the largest battery factory in the world. However, this level of production requires vast amounts of raw materials, particularly lithium, cobalt, and nickel.
Lithium is a key component of lithium-ion batteries, and its demand is expected to triple by 2025 due to the growth of the EV market alone. However, lithium supply is heavily concentrated in a few countries, such as Australia, Argentina, and Chile, which poses a significant risk to the supply chain. Moreover, the extraction of lithium can have negative environmental and social impacts, further complicating the future availability of this vital resource.
Cobalt is another critical material for battery production, but it faces even greater challenges. More than 60% of the world’s cobalt comes from the Democratic Republic of Congo (DRC), a country plagued by corruption, human rights abuses, and poor mining practices. The ethical and sustainable sourcing of cobalt is a pressing concern for battery manufacturers, and efforts are being made to develop alternatives or reduce dependence on this problematic resource.
Nickel is an essential component of high-energy-density batteries, which are crucial for long-range EVs and renewable energy storage. However, the supply of nickel faces potential constraints due to its scarcity and the increasing demand for batteries. Nickel prices have been rising steadily, prompting companies to explore alternative sources and develop more efficient battery chemistries that require less nickel.
The demand for battery raw materials is not limited to Tesla’s Gigafactory. Other major battery manufacturers, such as LG Chem, Panasonic, and CATL, are also expanding production to meet the growing demand for batteries. Additionally, various emerging sectors like grid-scale energy storage and portable electronics are contributing to the rising appetite for battery materials.
To address the impending supply cliff, experts suggest multiple strategies. First, recycling of lithium-ion batteries can significantly reduce the demand for raw materials. Currently, lithium-ion battery recycling rates are low, and developing efficient recycling technologies should be a priority. Second, manufacturers need to invest in research and development to find alternative materials or battery chemistries that are more abundant and environmentally friendly. Lastly, diversifying the supply chain and reducing dependence on a few countries is crucial for ensuring a stable and sustainable supply of battery materials.
The looming supply cliff for battery raw materials presents a major challenge for the growth of the EV and renewable energy industries. However, with proper planning, innovation, and sustainable practices, this challenge can be turned into an opportunity. By embracing recycling, investing in research and development, and diversifying the supply chain, the industry can continue its positive trajectory towards a cleaner and greener future.
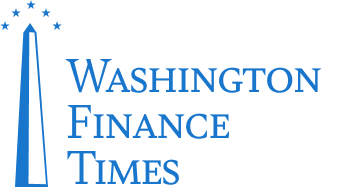